Chassis Welding Repairs: Techniques and Best Practices
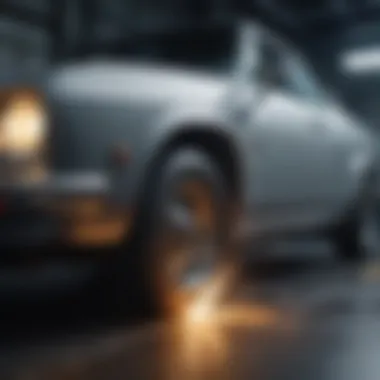
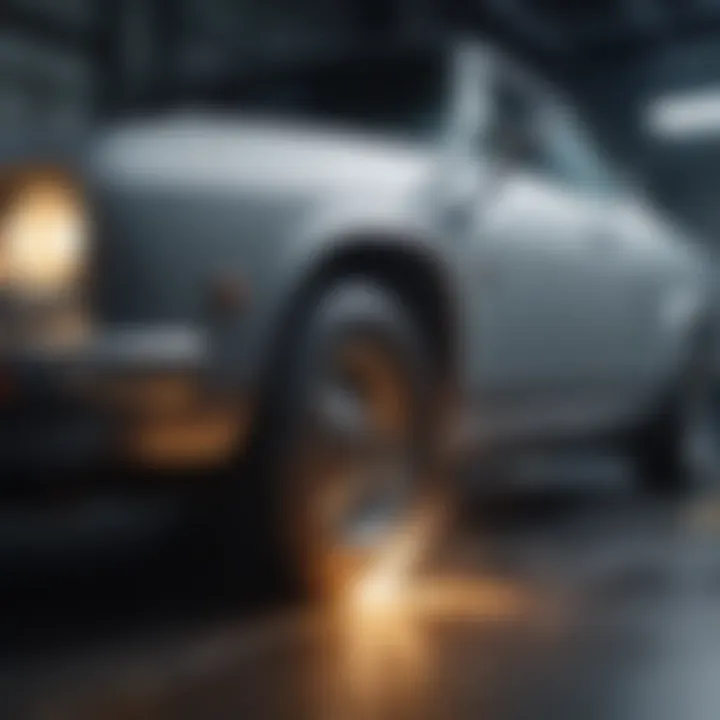
Intro
In the realm of automotive repairs, the chassis is like the backbone of a vehicle. When it suffers damage, the implications extend far beyond mere aesthetics; they touch on safety, performance, and longevity. Understanding the ins and outs of chassis welding repairs is therefore crucial. For enthusiasts and professionals alike, knowing which techniques to apply, what considerations to keep in mind, and the best practices for execution can mean the difference between a restoration done right and a botched job that compromises the vehicleโs integrity.
Welding is an art and a science. It requires a balance of technical skill and understanding of material properties. Chassis welding repairs often revolve around various techniques, with MIG welding and TIG welding standing prominent. The choice between these methods depends on factors such as thickness of the metal, desired strength, and specific application.
As we delve deeper into this topic, we will explore key techniques, outline essential materials for repairs, and dissect common pitfalls that one might encounter. Importantly, we will also touch on how recent market trends influence consumer choices in the realm of chassis repairs, helping you make informed decisions whether as a professional technician or an automotive hobbyist.
Let's begin with an examination of performance considerations that surround chassis welding repairs because understanding how repairs can affect the vehicle's overall performance is foundational.
Understanding Chassis Welding
Chassis welding is a fundamental aspect of automotive repair and restoration, acting as the backbone for any significant repair work done on vehicles. The importance of understanding chassis welding can't be overstated. It's not merely about affixing metal to metal; it's about ensuring the safety and performance of a vehicle. A well-welded chassis can vastly improve the structural integrity of a car, allowing it to endure rigors and stresses of everyday driving. If chassis repairs are not executed properly, it may lead to catastrophic failures down the road.
Moreover, chassis welding isn't just for fixing damages; it is also for enhancements and modifications. Whether you're aiming to enhance performance by lightening the chassis or adding more robust support for high-performance components, welding techniques play a vital role.
Understanding the nuances of this process provides automotive enthusiasts and professionals a sturdy foundation from which to build their multi-tiered repair and enhancement knowledge. This understanding addresses several key considerations:
- Type of welding technique appropriate for the material.
- Assessment and preparation of the chassis prior to welding.
- Safety precautions needed during the welding process.
- Evaluation of the overall structural integrity post-repair.
In essence, as we navigate through the various aspects of chassis welding repairs, keep in mind how essential a solid comprehension of this topic is for successful automotive repair.
Definition and Importance of Chassis Welding
Chassis welding involves the use of various welding techniques to join metal components of a vehicle's chassis. This process is crucial for ensuring the durability and safety of the vehicle, particularly in scenarios where the chassis has sustained damage. Essentially, the chassis serves as the vehicle's frame, and any imperfections can lead to severe consequences not just for the vehicle's performance but also for the occupants' safety.
The importance lies in its capacity to restore the vehicle to its factory specifications or improve upon them. A good chassis repair job maintains the structural alignment needed for optimal handling and stability. Thus, understanding this discipline is an indispensable part of any thorough automotive repair strategy.
Applications in Automotive Repair
In automotive repair, chassis welding finds numerous applications, extending beyond merely fixing a bent frame. The following are some key applications:
- Restoration Projects: Reviving classic cars often involves extensive chassis welding to restore structural integrity. This is particularly true for cars that have rust issues or have seen extensive collision damage.
- Modified Vehicles: Enthusiasts customizing their vehicles might need to modify the chassis for better performance or aesthetic appeal. This could involve fabricating new components and welding them in place.
- Safety Enhancements: For those involved in motorsports, reinforcing the chassis through welding can significantly improve safety during high-stress conditions.
- Repairing Damage: Accidents can lead to misaligned frames or damaged components. Expert welding can bring the chassis back to a functional state, thereby saving a vehicle from being deemed irreparable.
With various applications in mind, itโs clear that chassis welding is not just a technical skill but an art form that balances safety, performance, and design considerations.
Types of Welding Techniques
In the arena of chassis welding, understanding the different welding techniques is pivotal for achieving reliable repairs. Each method comes with its unique set of benefits and challenges, making it essential for automotive professionals to select the right technique for a given situation. The choice of welding technique can significantly influence the structural integrity and longevity of the vehicle. Through this examination, weโll delve into the prominent welding techniquesโMIG, TIG, Stick, and Flux-Coredโwhile also recognizing their specific applications and advantages in the context of chassis repairs.
MIG Welding
MIG welding, or Metal Inert Gas welding, stands out for its speed and ease of use. This method involves a solid wire electrode that is continuously fed through the welding gun. The wire melts and fuses with the base metal, creating a robust joint. One notable advantage of MIG welding is its versatility; it can weld a variety of metals and alloy types, from thin sheet metal to thicker components. It allows for high-speed welding, making it favorable for repairs that demand efficiency.
Benefits of MIG Welding
- Speed: MIG welding is quick, enabling the completion of repairs in less time.
- Ease of use: It is relatively easy to learn compared to other methods, attracting many new welders.
- Clean welds: With the right setup, MIG can produce clean and aesthetically pleasing welds.
MIG welding can be particularly effective for chassis repairs where there are multiple joints to work on quickly. However, itโs important to manage the heat input carefully to avoid warping thin sections of metal.
TIG Welding
TIG welding, or Tungsten Inert Gas welding, is often seen as the gold standard for high-quality welding. It involves a non-consumable tungsten electrode to produce the weld. The process is more intricate and requires a higher skill level than MIG welding, but the resulting welds are precise and can accommodate thinner materials without risking warpage.
Benefits of TIG Welding
- Precision: TIG produces high-quality, precise welds that can be crucial for critical chassis components.
- Control: Welders have better control over the heat, making it easier to forge integrity in thin materials.
- Versatility in metals: TIG can effectively weld a wide range of materials, including aluminum, steel, and copper alloys.
TIG welding can be more time-consuming compared to MIG welding, but the end results often justify the effort, especially in applications where safety and strength are paramount.
Stick Welding
Stick welding, also known as Shielded Metal Arc Welding (SMAW), has been a staple in welding for decades. It utilizes a consumable electrode coated in flux to produce the weld. This technique is particularly effective for outdoor projects, as its nature resists wind and fits a variety of environmental conditions.
Benefits of Stick Welding
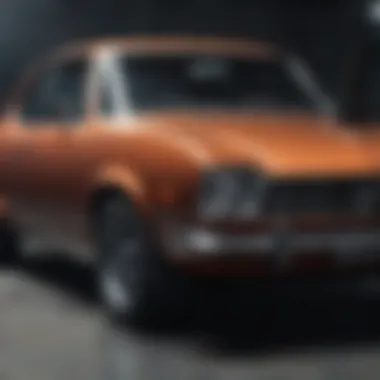
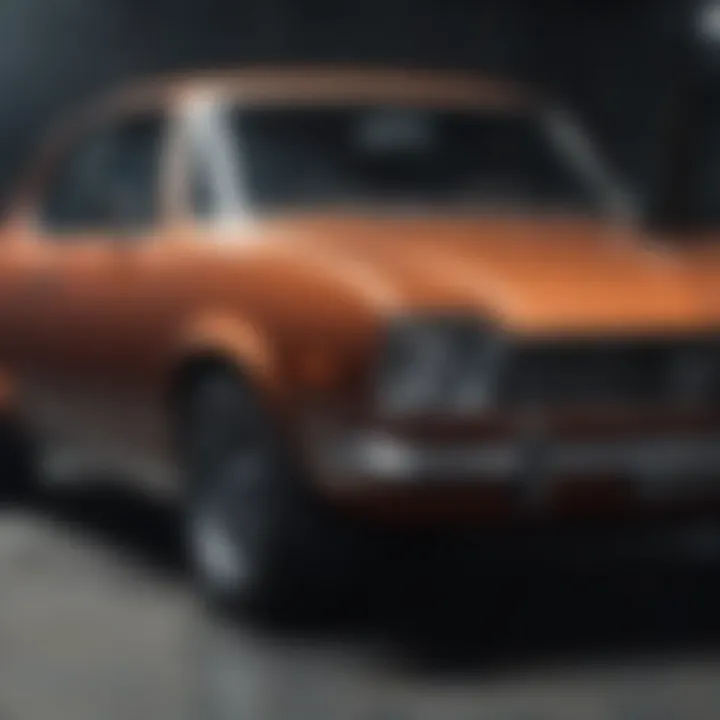
- Portability: Equipment needed for Stick welding is often less elaborate, making it easy to transport.
- Versatility: Can be used in outdoor conditions and on dirty metals where other methods might struggle.
- Cost-effective: Equipment and consumables for stick welding typically involve lower initial costs.
Though stick welding is robust, it can create more slag, which must be cleaned off for the best results. This could mean additional work, but for many, the reliability offered is worth it.
Flux-Cored Welding
Flux-Cored welding is somewhat similar to MIG welding, but instead of a solid wire, it uses a tubular wire filled with flux. This unique feature makes it possible to weld without the need for a shielding gas, which can be a deal-maker in windy conditions. Typical of a well-rounded welding approach, it strikes a balance between strength and usability.
Benefits of Flux-Cored Welding
- Self-shielding: This technique allows for welding in less-than-ideal conditions, enhancing adaptability.
- Deep penetration: It gives more penetration than MIG welding, making it suitable for thicker materials.
- Speed: Like MIG, it supports fast welding speeds, reducing overall time spent on repairs.
Flux-Cored welding is ideal when dealing with thick chassis components or in challenging environments. But, it's important to be diligent about the cleaning process afterward, as it may leave behind flux residue.
In summary, understanding various welding techniques allows professionals in the automotive sector to select the best approach for chassis repairs, ensuring safety and durability without sacrificing efficiency.
Materials Used in Chassis Welding
The materials chosen for chassis welding play a pivotal role in ensuring the longevity and strength of the vehicle. The chassis is like the backbone of a car, providing support and stability. Thus, selecting the right material can significantly affect safety performance, durability, and repair quality. In this context, understanding the various types of metals typically used, as well as how to assess their thickness, is essential for automotive professionals and DIY enthusiasts alike.
Types of Metals Commonly Welded
When it comes to chassis repairs, the metals that are most often welded together vary widely. Some common choices include:
- Mild Steel: This is perhaps the most widespread material used in chassis construction. It is affordable and welds well, making it a popular choice for repairs. Plus, it can absorb shocks and pressures, ideal for structural integrity.
- High-Strength Low-Alloy Steel (HSLA): This metal type offers a great balance of strength and ductility. It's used where extra strength is needed without adding too much weight. When welded, it requires careful consideration of heat input to avoid compromising its properties.
- Aluminum: While not as traditional as steel, aluminum is becoming more common in automotive chassis due to its lightweight nature. It's crucial to use compatible welding techniques, as aluminum requires more skill and specific equipment. But it can majorly contribute to fuel efficiency due to the reduction in overall weight.
- Stainless Steel: Known for its corrosion-resistant properties, stainless steel is a great option for parts exposed to harsh environments or moisture. It's a tougher material to weld because of its thermal conductivity, but the end result often justifies the effort.
- Composite materials: Increasingly, manufacturers are introducing materials such as carbon fiber reinforced plastics for certain chassis components. These are very light and have excellent tensile strength but can be challenging to repair and require specialized techniques.
Understanding these materials helps in making informed choices during repairs. Each metal has distinct characteristics that can either enhance or detract from the overall strength of a weld.
Assessing Metal Thickness
Assessing metal thickness is a critical step in the welding process. The thickness of the metal influences the choice of welding technique, the welder settings, and the process itself. Here are some key points to consider:
- Calibration is Key: Before commencing any welding, itโs vital to assess the thickness accurately. Using a micrometer or caliper can help gauge the thickness to within a thousandth of an inch. This ensures you know exactly what you're working with.
- Welding Method Matters: Thicker materials typically require different welding approaches than thinner ones. For instance, using MIG might be suitable for 1/4 inch or thicker steel, whereas TIG could be preferred for thinner sections due to its precision.
- Weld Penetration: Thicker materials will require deeper penetration to ensure a proper bond. A welder experienced in working with various thicknesses can adjust settings like voltage and wire feed speed to achieve optimal penetration without burning through the material.
- Thin Metal Considerations: When welding thinner metals, the risk of warping increases. Keeping the heat input lower and stitch welding can prevent warping, which could compromise the integrity of the chassis.
- Consulting Material Specifications: Many manufacturers provide specifications on the materials they use. Familiarizing oneself with these details allows for better judgment in repair decisions.
Understanding the types of metals and how to assess their thickness effectively informs technicians on the best practices for chassis welding repairs. Itโs all about making choices that not only meet industry standards but also enhance the vehicle's performance on the road.
"In the world of automotive repair, knowing your materials can make the difference between a quick fix and a solution that lasts."
Welding is much more than just joining two pieces of metal. Itโs about creating a bond that withstands the test of time and the strains of travel. ๐ ๏ธ
For those looking to dive deeper into metallurgical properties or specific welding techniques, resources like Wikipedia and Britannica can provide additional insights.
Preparation for Chassis Welding Repairs
Preparation plays a pivotal role in the success of chassis welding repairs. A lack of adequate preparation can lead not only to inefficient repairs but also to safety hazards that might compromise the structural integrity of the vehicle. When it comes to chassis welding, preparation covers multiple facets including safety precautions, tool selection, and understanding the specific work environment. Failing to address these aspects is like trying to bake a cake without reading the recipeโit's bound to create a mess rather than a masterpiece.
Ensuring proper preparation can make the difference between a quick fix and a repair that stands the test of time. From setting up the workspace to compiling a checklist of necessary tools, every small detail contributes significantly to the overarching success of the project. If the groundwork isn't laid, the entire welding process may be fraught with challenges that could have been easily avoided.
Safety Precautions
Safety should top the list when preparing for chassis welding repairs. The risks involved are not trivial. Welding produces intense heat, potentially hazardous fumes, and splatter that can cause burns or injuries if proper precautions are not taken. Hereโs a rundown of essential safety measures:
- Personal Protective Equipment (PPE): Every welder should gear up with suitable PPE, including gloves, goggles, and flame-resistant clothing. This barrier against burns and eye damage is fundamental.
- Adequate Ventilation: Carbon monoxide and other fumes can accumulate quickly during welding. Working in a well-ventilated area or using a fume extraction system helps to mitigate this risk significantly.
- Fire Safety: Keep a fire extinguisher nearby and remove any flammable materials from the work area. An ounce of prevention can prevent a pound of disaster.
- Area Awareness: Ensure the workspace is free of clutter and obstacles. This not only increases safety but also improves efficiency.
"When it comes to welding, safety is not just a precaution; it's a responsibility."
Tools and Equipment Required
Having the right tools on hand is as crucial as understanding welding techniques. The right equipment ensures that repairs can be executed smoothly and effectively. Hereโs a checklist of must-have tools for chassis welding:
- Welding Machine: Depending on the technique being employed (MIG, TIG, etc.), a suitable welding machine is vital. Opt for one that matches the thickness and type of metal.
- Welding Filler Rods or Wire: Make sure to select the appropriate filler material that is compatible with the base metal being welded.
- Clamps: These help hold components in place while welding, ensuring everything remains aligned and secure.
- Grinder: A good angle grinder is necessary for surface preparation and cleanup after welding. This will facilitate cleaner welds and smooth out rough edges.
- Measuring Tools: Having a tape measure, square, or calipers handy assists in achieving precise joints and alignments.
- Protective Gear: Always have a full-face shield, gloves, and protective clothing ready.
With a well-stocked toolbox and a solid plan in place, you're well on your way to executing effective chassis welding repairs. Proper preparation is the bedrock upon which successful projects are built.
Diagnostic Techniques for Chassis Issues
Understanding chassis issues is crucial for the safety and performance of any vehicle. Chassis problems can manifest in various ways, often going unnoticed until they reach a critical stage. This is where diagnostic techniques come into play, serving as a first line of defense in detecting inefficiencies before they become costly repairs or, worse, safety hazards.
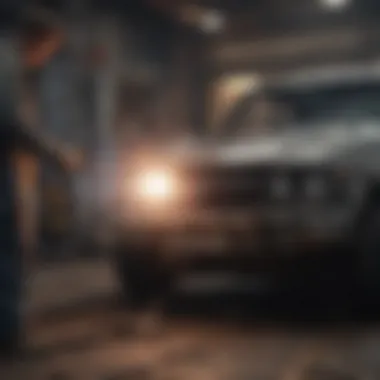
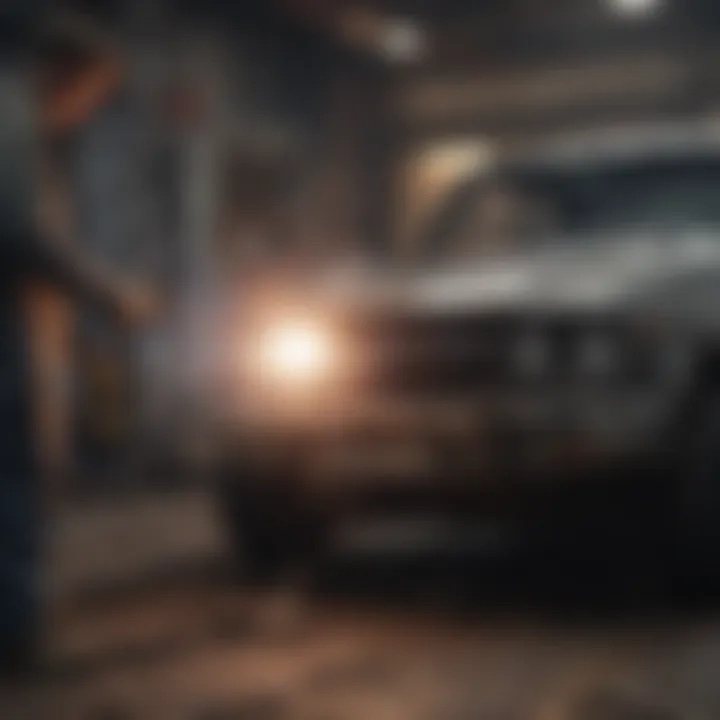
By employing robust diagnostic methods, automotive professionals can pinpoint the exact nature of the problem, enabling targeted repairs. This not only saves time and materials but enhances the longevity of the vehicle itself. The art of diagnosis blends both traditional knowledge and the latest technological advancements, making it an essential area within chassis repair.
Visual Inspection Methods
Visual inspection is the bread and butter of chassis diagnostics. It allows mechanics to gather initial information without any special tools. Here, the eye becomes the primary tool.
When examining the chassis visually, several key elements should be considered:
- Surface Cracks: Look for cracks or stress fractures, which might indicate underlying structural issues.
- Worn Components: Parts like bushings, mounts, and joints should be checked for excessive wear, which can compromise safety.
- Corrosion: Rust can be an enemy to the integrity of a chassis. Inspect areas that are prone to moisture entrapment carefully.
- Alignment and Geometry: A simple visual alignment check can reveal if the suspension or frame is out of place.
"A thorough eye can catch what a mechanical gauge might miss."
The importance of systematic visual checks cannot be understated. Not only do they help in the initial diagnosis, but they can also inform the mechanic about the vehicleโs history and how it was maintained.
Using Diagnostic Tools
While visual inspections provide a snapshot, diagnostic tools bring a deeper understanding of the chassisโ state. Modern technology such as computerized diagnostic scanners, ultrasonic testing devices, and magnetic particle inspection can shine a light on issues that are otherwise hidden.
Some commonly used diagnostic tools include:
- OBD-II Scanners: These can read trouble codes and provide insights into the vehicleโs electronic systems that may affect the chassis.
- Alignment Tools: Devices like laser alignment systems help in ensuring that all components are in harmony with one another, which is critical for performance and safety.
- Ultrasonic Thickness Gauges: These tools are helpful in assessing the integrity of parts, particularly where corrosion might be a concern.
- Cameras for Inspection: Specialized cameras can reach tight spots, making it easier to identify wear and damage.
By employing a combination of visual checks and advanced diagnostic tools, a mechanic can create a holistic picture of the chassis condition, leading to informed decisions about necessary repairs. In a world of evolving automotive technology, staying ahead of diagnosis can make all the difference in maintaining safety and functionality.
Common Challenges in Chassis Welding
Chassis welding isnโt a walk in the park. Itโs fraught with challenges that can make or break a repair job. Understanding these obstacles is crucial for anyone in the automotive field. There are several key elements to keep in mind when dealing with chassis welds. These include hidden damage that may not be visible at first glance, the inevitable corrosion of metal, and the ever-present alignment issues that can arise.
Addressing these challenges head-on ensures that repairs are effective and long-lasting, ultimately contributing to a vehicleโs safety and performance.
Identifying Hidden Damage
Often, the most significant problems in chassis welding arise from hidden damage. While a visual inspection might reveal cracks or bent frames, some issues lurk beneath the surface. The frame can be weakened by previous accidents, and understanding the full extent of such damage is crucial.
To uncover this hidden damage, technicians might need to employ various methods. Tools like ultrasonic testers or X-ray machines can come in handy. These technologies help in identifying structurally compromised areas without having to tear the entire chassis apart.
Being thorough in this assessment can avoid costly mistakes down the line. If a technician misses hidden damage, the integrity of the entire repair can be compromised. Itโs a classic case of, "out of sight, out of mind," which shouldnโt happen in chassis repairs.
Dealing with Corrosion
Corrosion is like a sneaky thief; it eats away at metal silently, and by the time you notice it, it could be too late. Almost every vehicle with some age shows signs of this, especially in areas exposed to moisture or salt.
When considering repairs, itโs vital to tackle corrosion head-on. This can involve using wire brushes, sanders, or chemical rust removers to treat affected areas before welding. In some cases, repair might mean replacing entire sections of metal if the corrosion is too severe.
Itโs worth mentioning that even minor rust can lead to structural issues later if not addressed properly. So, catching corrosion early can save both time and trouble later on. Itโs a matter of ensuring that the chassis remains solid and safe for whatever comes its way.
Alignment Issues
Alignment issues are another persistent thorn in the side of chassis welding. When a vehicle takes a hit, the frame may warp, leading to misalignment. This can severely affect how the vehicle handles and its overall safety.
Proper alignment is not just about sticking a few parts back together; it requires precision. Using alignment jigs or measuring tools can help ensure everything lines up perfectly. Misalignment can be a monster, not just making repairs ineffective, but also increasing the risk of further damage and even accidents on the road.
If you ever had a feeling of a car pulling to one side while driving, it might be a direct result of poor alignment post-repair. Getting this right means taking the extra time to measure twice and cut onceโnot just a clichรฉ, but a rule to live by in chassis welding.
"Alignment isnโt just a technical term; itโs a promise to the driver that their vehicle operates as it should."
In summary, the challenges faced in chassis welding like identifying hidden damage, dealing with corrosion, and ensuring proper alignment are pivotal. Proper care in addressing these issues fosters superior repairs and enhances vehicle safety and longevity. A proactive approach is the ticket to mastering chassis welding.
Testing Structural Integrity Post-Welding
Testing the structural integrity of a chassis after welding is not merely a routine step; it is an essential one that can determine the safety and longevity of the vehicle. After welding, there's always a question mark about whether the repairs will hold under stress and whether the vehicle is back to its original operational capability. Left unchecked, inferior welding can lead to catastrophic failures, potentially endangering lives.
By ensuring that welding quality meets safety standards, one can mitigate risks that might arise from undetected faults. Itโs like double-checking your work before handing it in for grading; it guarantees that you know your effort is robust and dependable.
There are a few key elements to consider when evaluating the structural integrity post-welding. These include:
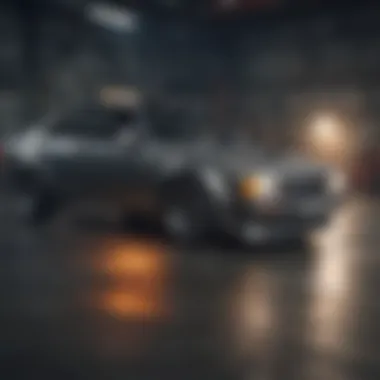
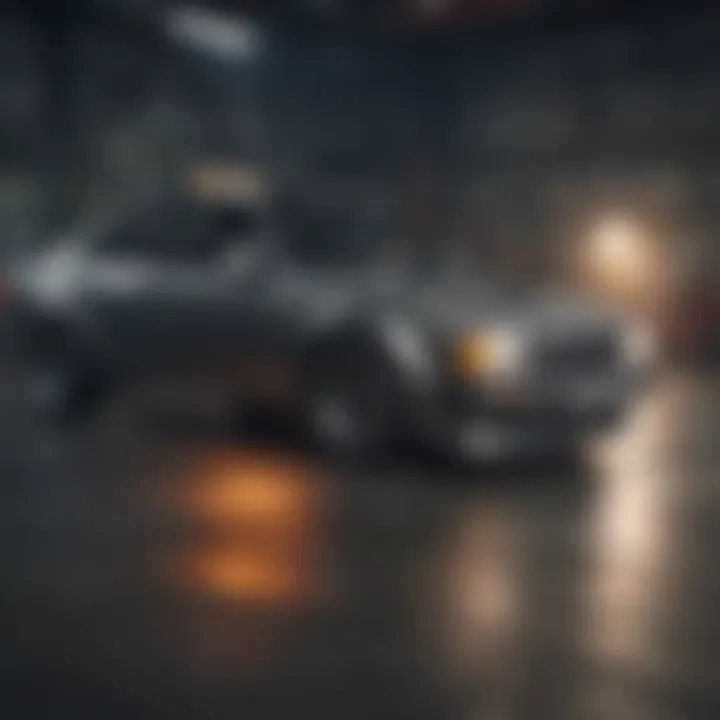
- Assessment of Welding Quality: A thorough inspection helps confirm that the welds exhibit sufficient penetration and proper bead shape.
- Checking Alignment: Misalignment can affect how the chassis handles on the road. Misaligned welds are often the root of long-term issues.
- Metal Fatigue Evaluation: Since metal properties can change post-welding, assessing fatigue is vital for predictability in performance.
Given the stakes involved, both safety and financial, these checks are crucial, underscoring the importance of diligence in the post-welding phase.
Visual Checks for Welding Quality
Visual inspection offers a first line of defense in ensuring that the soldering is solid. Skilled technicians look for specific indicators that suggest the integrity of the welds. Key aspects to scrutinize include:
- Bead Quality: A bead that is too thick or too thin may indicate issues with technique. An ideal bead should appear uniform.
- Surface Cracks or Porosity: These defects indicate that there may have been issues either with the welding parameters or the cleanliness of the base metals before welding.
- Consistency Across Joints: Every weld should have a semblance of uniformity and consistency; disparities can indicate potential failures.
This immediate visual evaluation can save both time and money. If problems are spotted early, it may help prevent deeper complications that could arise down the line. Don't underestimate the benefit of a second pair of eyes during this stage; consultation amongst peers can offer alternative perspectives.
Non-Destructive Testing Methods
Non-destructive testing methods, or NDT for short, are a pivotal component of post-welding assessment. They allow technicians to examine the welded joints without compromising the integrity of the work. This kind of testing can uncover hidden issues that might otherwise go unnoticed by visual checks alone. These methods are particularly invaluable in identifying internal inconsistencies or weaknesses.
Several approaches are commonly used in non-destructive testing:
- Ultrasonic Testing: This method employs high-frequency sound waves to detect flaws in the weld. If there are inconsistencies or voids, the sound waves will behave differently than expected.
- Magnetic Particle Testing: This technique is effective for identifying surface and near-surface defects in ferromagnetic materials. Magnetic particles adhere to the surface flaws and reveal them visibly.
- Dye Penetrant Testing: A colored dye is applied to the surface, and after a set period, it is wiped off. Any detectable flaw will retain the dye, making it visible.
Using NDT techniques, repair professionals can gain an insightful perspective on the integrity of welds without the risk of degradation. It also serves as peace of mind for both technicians and vehicle owners alike.
"Remember, the strength of a chassis isn't just about how it looks on the outside; it reflects whatโs happening beneath the surface too."
Overall, testing for structural integrity post-welding is a comprehensive process that goes much further than a simple visual inspection. It ensures safety, reliability, and longevity in vehicle operation.
Market Trends and Consumer Preferences
Market trends in the realm of chassis welding are as dynamic as the vehicles themselves. Understanding these trends is crucial for stakeholders, not just to stay competitive but also to align with the preferences and expectations of consumers. In an era where technology advances at lightning speed, keeping abreast of market movements helps automotive professionals make informed decisions about service offerings and operational practices.
As automotive technology evolves, so do the expectations consumers hold for chassis repair services. Efficiency, quality, and sustainability come to the forefront. Clients are not just looking for a quick fix; they want assurance of durability and safety. Given the potential hazards of poorly executed chassis repairs, prioritizing these elements can enhance customer trust.
Current Trends in Chassis Repair
A few significant trends have emerged in the chassis repair sector, shaping the landscape dramatically:
- Increased Use of Robotics: Automation in welding processes is becoming more commonplace. Robots can ensure precision and repeatability, which are challenging to achieve through manual labor. They minimize human error and improve overall welding quality.
- Sustainability Practices: The shift towards environmentally-friendly materials and processes is gaining traction. Automotive repair shops are now adopting practices that not only align with sustainability goals but also cater to eco-conscious customers. This might include using recycled materials or energy-efficient welding equipment.
- Digital Integration: The integration of technology into the repair process is on the rise. Using software for diagnostics and repair tracking enhances transparency and communication between the shop and the customer. Customers expect real-time updates on their vehicle status, shifting the focus toward customer-centric practices.
- Multimaterial Body Structures: As new vehicles move toward mixed-material construction, chassis repair methods must adapt to handle welding with diverse materials such as high-strength steel and aluminum. This complexity requires repair shops to invest in training and equipment that can manage these changes.
Consumer Expectations and Satisfaction Metrics
When diving into consumer expectations, clarity and quality reign supreme. Customers today are armed with more information than ever before, thanks to the vast online resources available. Here's what consumers generally expect from chassis repair services:
- Transparency: Clients desire clear communication about the processes involved in the repair. They appreciate detailed explanations about repairs being done and the technologies used.
- Timeliness: In a world bustling with commitments, time is an ever-valuable commodity. Customers expect repairs to be completed efficiently without sacrificing quality.
- Post-Repair Support: Good service doesn't end with the handover of the vehicle. Consumers increasingly look for warranties on repair work and advice on maintenance to ensure long-term satisfaction.
- Comprehensive Reviews: With platforms like Reddit and Facebook, consumers heavily rely on reviews and recommendations from fellow vehicle enthusiasts. Shops that excel in customer service and quality repairs often garner favorable online reputations.
The automotive industry is not just about vehicles; it's about relationships. Building trust and understanding who your clients are is a pivotal element of the equation.
In summary, the landscape of chassis repair is continually transforming, influenced by technological advancements and shifting consumer preferences. Understanding these dynamics not only improves service quality but also fosters deeper relationships with clients, ultimately leading to loyalty and sustained success.
Future Directions in Chassis Repair Technology
As we navigate the fast-paced world of automotive repair, understanding the future directions in chassis repair technology is paramount. The evolution of this field is not just about keeping pace with trends but adapting to the dynamic demands for safety, efficiency, and sustainability. This section highlights critical elements and benefits that are likely to shape the landscape of chassis welding repairs in the coming years.
In this article, we'll explore how emerging technologies and innovations are revolutionizing repair processes. Such advancements are not merely enhancing existing methods; they're redefining standards. By adopting these new techniques and tools, repair professionals can increase precision, reduce labor costs, and ultimately elevate the safety standards of vehicles.
Emerging Welding Techniques
The landscape of welding is continuously evolving, and various innovative techniques are coming to the forefront. Among these, robotic welding stands out. With precision at its core, robotic applications ensure consistent weld quality and speed. This technology minimizes human error and enhances the structural integrity of the chassis. For tackle intricate designs or difficult-to-access areas, advancements in laser welding provide the ability to work with thinner materials while ensuring a robust bond.
More traditional techniques, like MIG and TIG welding, are also being modified to incorporate computer-assisted processes. These smart adaptations not only improve weld quality but also provide data telemetrics to track the welding conditions and results over time. This is crucial for understanding long-term performance and wear in repaired chassis.
Benefits of Emerging Techniques
- Increased Efficiency: Automation speeds up the welding process, allowing for more vehicles to be repaired in less time.
- Enhanced Precision: Advanced methods ensure more precise welding, reducing the likelihood of future issues stemming from poor repairs.
- Sustainability: Many new welding techniques produce less waste, aligning with a growing push towards greener practices in the automotive industry.
Impact of Technological Advancements on Repair Processes
Technological advancements are not just trickling down into welding but are also reshaping the repair processes as a whole. Consider the emergence of diagnostic tools, such as ultrasonic testing equipment, which allows for real-time assessments of chassis integrity before, during, and after repairs. This technology leads to better-informed decisions, as it provides immediate feedback on the structure's health without the need for destructive tests.
Moreover, utilizing augmented reality (AR) in training and repair can be a game changer. Technicians can visualize complex welding tasks overlaid on real-world frames, enhancing their understanding and execution of repairs. This immersive experience emphasizes correct methods and reduces the chances of mishapsโcritical when working with the vital part of a vehicle's structure.
"Technological advancements in chassis repair are not merely advantageous; they're essential in ensuring the safety and efficiency of modern vehicles."
As these technologies become more commonplace, their influence can lead to standardized best practices across the industry. By implementing newer methods, workshops can not only elevate their service levels but also boost their reputation among tech-savvy consumers looking for reliable and quality repairs.